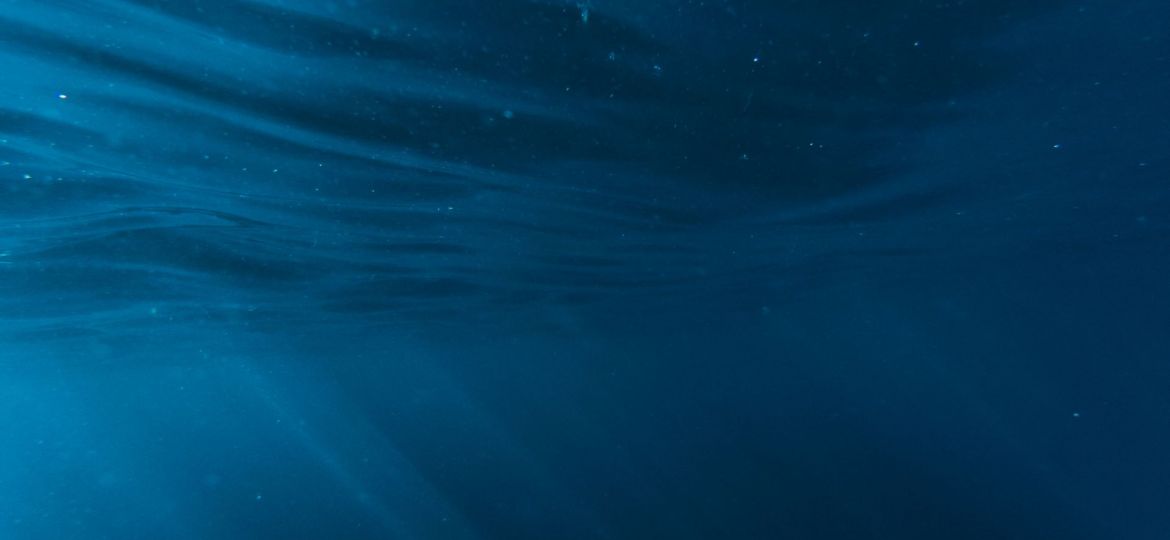
3d imaging: an essential solution to the challenges of underwater inspections
Underwater 3D imaging is emerging as an essential solution to the challenges of inspection in hostile environments, where visibility is often reduced and accuracy is crucial. This technology makes it possible to generate detailed, realistic models of submerged structures, providing operators with a complete, usable view. It is particularly well suited to, and even necessary for, conclusive inspection of critical components whose degradation can lead to costly production shutdowns or severe environmental risks.
Among its most common applications, 3D imaging excels in the inspection of offshore infrastructures such as oil, gas and wind platforms. It enables a detailed assessment of jackets, mooring chains, flex joints, manifolds and pipelines. These inspections are essential to guarantee the integrity of these infrastructures and prevent potential malfunctions or, worse, industrial and environmental disasters.
In addition to these established use cases, 3D imaging paves the way for new applications that are still underexplored by competitors, enabling operators to achieve greater precision and efficiency. For instance, jumper metrology is crucial to ensure optimal alignment and precisely define the connector dimensions between two pipeline segments. Similarly, the assessment of marine growth on submerged structures can be carried out with a very high degree of accuracy: thanks to detailed analysis using Computer-Aided Design (CAD) tools, it becomes possible to precisely measure the mass or volume of these organisms. This is especially relevant for determining the impact of such deposits on structural stability, monitoring their evolution over time, or planning for decommissioning.
Moreover, 3D imaging plays a key role in planning repairs, monitoring the condition of installations after interventions, and preventive maintenance. By capturing highly detailed and complex phenomena, such as corrosion, it not only helps optimize underwater operations but also extends the lifespan of infrastructures while reducing maintenance costs and operational risks.
simplicity meets precision: a flexible and efficient 3d solution for underwater inspections
When it comes to 3D imaging, the commonly recommended and intuitive solution is to use two cameras, modelled on the stereoscopic vision of the two human eyes, to appreciate depth. This may seem like a natural choice, but it has a number of major drawbacks: a bulky and complex system necessary for generating 3D data, requiring meticulous pre-calibration; several components have to be installed in the often limited space of underwater inspection vehicles, and a very high cost. These limitations can be problematic in demanding underwater environments where simplicity and robustness are key.
That’s why a single-camera solution would be a much more advantageous alternative.
Such solution exists ; it relies on photogrammetry, a powerful technique that reconstructs 3D models from images captured at different angles by a single camera—without compromising the model’s accuracy. Photogrammetry precisely calculates the shapes, dimensions and volumes of objects using only the visual data from a single camera, without the need to synchronize multiple sensors.
This approach offers a major additional advantage: adaptability to unplanned needs. Indeed, it can be unpredictable whether 3D modelling during an underwater inspection is needed. With a complex stereoscopic system, a dedicated equipment has to be prepared, calibrated and installed before the mission. A photogrammetric camera, on the other hand, simply records a video stream at any time and then reconstruction of the 3D model is performed from data captured. This flexibility, combined with the simplicity and accuracy of the system, makes it an ideal solution for capturing high-quality 3D data, without the constraints of a bulky, costly setup.
orpheoscan: the i2s solution
i2S has a long-standing expertise in photogrammetry, particularly for medical applications. We have leveraged this expertise to enhance the Orphie range of underwater cameras—renowned for their unmatched image quality—with a 3D modelling solution called OrpheoScan, a technology that pushes the boundaries of underwater imaging precision. Our Orphie camera stands out for its ability to see up to three times further than standard cameras on the market, even in turbid waters where visibility is usually compromised. With this unique performance, we are able to achieve measurement results of our 3D models with a tolerance of 0.3 mm and an accuracy of 2sigma, offering detailed and reliable results for the most demanding inspections. Our solution is simple and flexible: a single standard Orphie camera is all you need. There is no need to plan and install a complex setup before the inspection operation.
When 3D modelling becomes necessary, you simply record a video stream during the ongoing inspection. From this video, a precise 3D model of the inspected structure is then produced. This approach, combining performance, simplicity, and adaptability, enables our clients to quickly and efficiently obtain actionable data while reducing the cost and complexity of underwater operations.